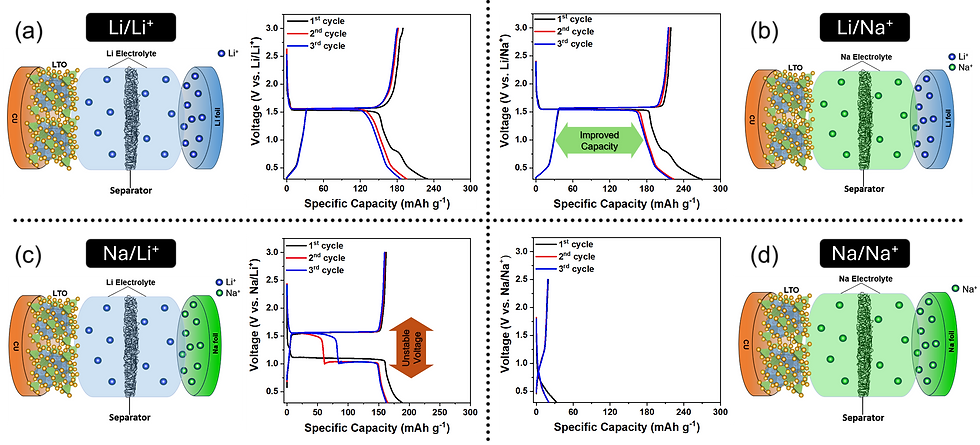
Li4Ti5O12 (LTO) is a highly promising anode material for both Li-ion and Na-ion batteries due to its remarkable structural stability, minimal volumetric expansion, and high safety. Despite extensive research on LTO performance in conventional systems, little attention has been given to its behavior in mismatched electrolyte environments. This study explores the electrochemical behavior of LTO anodes in Na⁺-containing electrolytes for Li⁺/Na+ intercalation, providing new insights into ion intercalation mechanisms and enhancing battery performance. Using different counter electrode and electrolyte configurations, we reveal that LTO exhibits superior capacity and cycle stability in a mismatched Li/Na⁺ environment compared to the standard Li/Li⁺ system, delivering capacities of up to 219 mAh g−1. Electrochemical and structural analyses indicate that enhanced performance stems from the unique interaction between Li⁺/Na⁺ and LTO structure, leading to improved charge-discharge performance. Additionally, the Na/Li⁺ configuration displayed unique behavior, where a distinct plateau splitting emerged after the first cycle, indicating complex ion interactions that ultimately affect cycling stability. These findings not only highlight the potential of LTO anodes in mismatched electrolyte systems but also offer a pathway toward more cost-effective and sustainable energy storage solutions by leveraging sodium-ion electrolytes in place of traditional lithium-based systems.
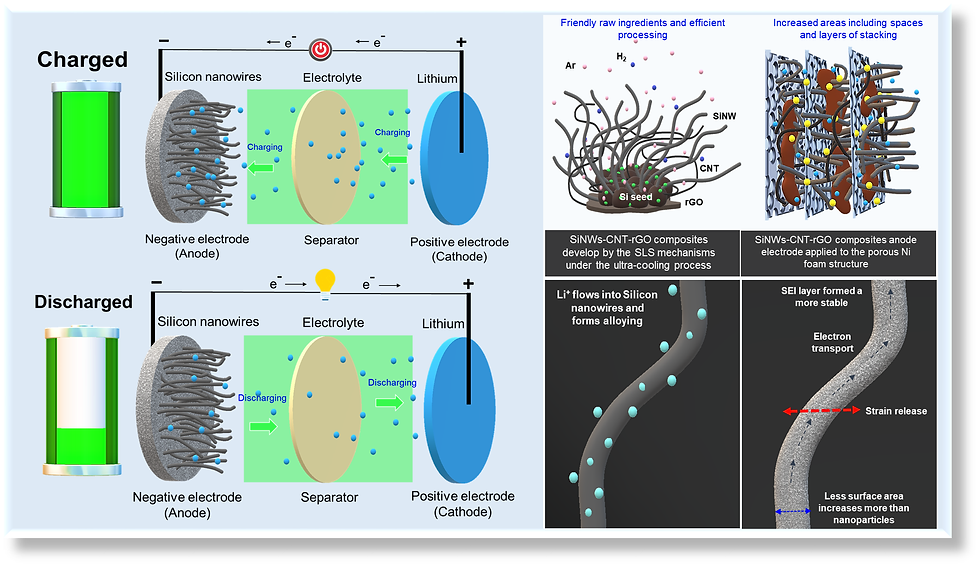
Silicon nanowires (SiNWs) address key challenges associated with traditional silicon anodes in lithium-ion batteries (LIBs) by mitigating pulverization and providing efficient ion transport pathways. However, their high fabrication cost and poor structural stability remain significant obstacles. This study presents a novel SiNW-CNT-rGO composite fabricated via a solid-liquid-solid (SLS) growth mechanism using NiO/Ni catalysts to establish a 3D conductive network. The composite integrates carbon nanotubes (CNTs) and reduced graphene oxide (rGO) to enhance electrical conductivity and stabilize the solid electrolyte interphase (SEI). Embedding the composite in 3D nickel foam (NF) further improves structural integrity and enhances Li+ ion diffusion, outperforming conventional copper foil (CF) current collectors in capacity across various rates. The integrated design provides efficient electron and ion transport pathways while mitigating mechanical stresses. Electrochemical evaluations reveal that the SiNW-CNT-rGO@NF anode significantly improves specific capacity, cycling stability, and rate capability compared to SiNW-based anodes with CF. These findings reveal the potential of the 3D SiNW-CNT-rGO@NF architecture as a scalable and cost-effective solution for next-generation high-performance LIBs.

The occurrence of Coulombic efficiency (CE) troughs in silicon (Si) anodes for lithium-ion batteries (LIBs) presents a critical yet overlooked concern that could lead to battery failure in full cells. Here we conduct a comprehensive investigation into this previously unreported phenomenon. Factors influencing CE trough occurrence and severity, including electrode thickness, Si particle size, cycling rate, electrolyte composition, and voltage window, are systematically examined. Experimental results demonstrate that thinner electrodes and slower cycling rates accelerate CE trough onset, whereas employing a THF-based electrolyte or a narrower voltage window (0.01-0.5 V) results in stable electrochemical performance without CE troughs, concurrently with the presence of LixSi. Structural analysis via HAADF-STEM and SEM reveals a close association between CE trough severity, electrode volume expansion, and delamination, influenced by the formation of a sponge-like structure and SEI stability. These findings yield valuable insights into CE trough mechanisms and provide guidance for mitigating their occurrence through electrode design, electrolyte selection, and operational parameters, thereby advancing high-performance LIB development. Future research directions involve exploring the role of SEI components and alternative electrolyte additives to enhance SEI stability and mitigate CE troughs.